
Making Sustainability Happen.
Discover Our Solutions
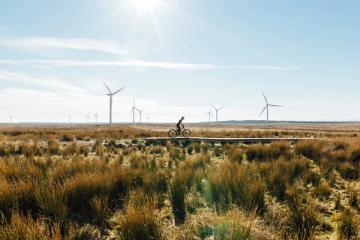
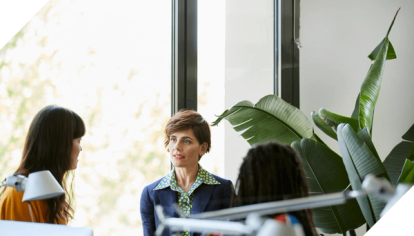
Organisations across the world today are facing unprecedented pressure to take an active part in creating a more sustainable and just future.
SLR exists to support clients on this journey. Our strategic, engineering and technical teams take the pain out of navigating the ever-shifting context of sustainable business and support you in Making Sustainability Happen.
Full-Spectrum Solutions
We are specialists in our field, able to offer clients full-spectrum sustainability strategy through to project delivery support. This enables us to help clients tackle the greatest sustainability challenges they face today.
Learn more about our process-
Strategy & Performance
-
Sustainability Challenges
-
Project Delivery
Working at SLR
SLR is committed to creating and sustaining a global, inclusive culture, where differences are embraced for the benefit of our people, our clients and the communities around us.
Careers at SLR-
100+
Office Locations
-
One Team
SLR’s One Team culture is the backbone of our organisation. Our strength not only comes from our skills and experience, but also from our ability to collaborate across disciplines and regions - supporting each other on a global basis.
-
3000+
Global Colleagues
-
3 Year
Strategic Goals
-
DE&I
Our Diversity, Equity & Inclusion strategy will help us achieve our organisational and people goals, supporting our future strategic direction and growth, and our One Team culture. It provides a shared direction and commitment for the organisation so we can work together to respect and value our diverse workforce and continue to build a more inclusive workplace.
-
4 Key
Commitments to Make it Happen
-
45+
Technical Disciplines
-
Careers
We don’t have all the answers to the complex sustainability challenges faced by humanity today. But we’re working on it. When you join SLR, you’ll work alongside some of the world’s leading advisors and technicians on projects of global importance in the environmental space.
-
6
Operating Regions
Latest Thinking
-
Strengthening Supplier Engagement: 5 ways companies can facilitate their suppliers’ transition to enhanced ESG performance
by Chynna Pickens
View post -
A Sound Decision: Selecting the Right Acoustic Treatment for Your Architectural Project
by Ben Adler
View post -